Introduction
Electrospinning is a versatile technique that extrudes a polymer solution in a high-voltage field to fabricate fibers on the micro to nanoscales. Unlike other fiber production techniques, electrospinning can easily tune the fiber diameter (100 nanometers to a few micrometers), mechanical properties, and chemical functionality. While this technology shows promise within research settings, it is often believed that the process is not scalable and therefore not appropriate for industrial applications.
Electrospinning is a viable technique for scaling up the production of fiber mats for commercial applications. This was recently demonstrated by Bionicia during the Covid-19 era when electrospun N95 facemasks were fabricated with a production rate of about 300,000 masks per day. When increasing the throughput of electrospinning from a benchtop research grade instrument to a higher throughput production scale system, several key parameters must be tuned to fabricate consistently high-quality fibers. The key parameters to consider are solution properties, environmental conditions, applied voltages, flow rate, needles, and collectors.
Electrospinning Solution Properties:
Various solution properties will impact the formation of electrospun fibers and must be optimized to ensure consistent fabrication. Measuring and maintaining these properties is critical for ensuring that the electrospinning process produces consistent fibers. It is also necessary to ensure that these properties do not deviate during the upscaling process.
Surface Tension:
The formation of the Taylor cone, a key step in electrospinning, is influenced by the surface tension of the solution. A higher surface tension usually requires a higher applied voltage to create a Taylor cone jet. If the surface tension is too high, then the electrospinning process will be hindered, and the final product may have uneven fibers, beaded fibers, or in extreme cases no fibers are formed. Conversely, if the surface tension of the solution is too low, then a Taylor cone won’t form, and the solution will generate droplets during electrospinning. The surface tension of the solution should be measured using a Tensiometer (force or optical) and kept consistent throughout the scale-up process.
Viscosity:
Viscosity is a key property that measures a fluid’s resistance to flow. A solution that is too high or too low in viscosity will impede the upscaling process and prevent the production of electrospun fibers. If the viscosity is too high, the required force to flow the solution will be too high and prevent a proper Taylor cone from forming. A viscosity that is too low will create drips and may not consistently generate a Taylor cone. The viscosity of the solution should be measured with a viscometer and tuned appropriately.
Conductivity:
Conductivity is the measure of how easily a material conducts electricity. This determines how easily charges can be transported to the surface of the electrospinning jet which plays a critical role in the morphology of the resulting fibers. Conductivity can be measured using a conductivity probe.
Volatility:
During the fabrication of electrospun fibers, the solvents evaporate as the polymer travels to the collector. The rate of this evaporation will impact the electrospinning process, fiber size, and fiber morphology. A solvent that is too volatile can be prone to excessive needle clogging and prevent a continuous electrospinning process. Too low in volatility means the solvent doesn’t fully evaporate and causes the polymer to land partially wet, which impacts the overall fiber morphology. The evaporation rate for different polymer solutions can be tuned by choosing an appropriate solvent or by mixing various high and low-boiling-point solvents at different ratios.
Environmental conditions:
Control of the environmental conditions is critical to the consistent formation of electrospun fibers. Temperature and relative humidity impact how the solvent evaporates during fiber formation are among the most critical environmental conditions to monitor and maintain. Deciding on the appropriate temperature and humidity conditions will depend on the desired fiber properties.
Temperature:
Temperature impacts the viscosity of the electrospinning solution and the rate of solvent evaporation. Higher temperatures generally result in lower solution viscosity and faster solvent evaporation. This is not always a negative effect, as faster solvent evaporation is helpful when forming larger fibers. However, if smaller fibers are needed, a slower evaporation rate would be preferred. If the solution is prone to causing a chemical reaction, a higher temperature may also result in an undesirable chemical reaction.
Humidity:
Humidity affects the rate of solvent evaporation and the surface tension of the electrospinning solution. Higher humidity can lead to slower solvent evaporation and higher surface tension. This can make it more difficult to process the solution and can alter the fiber diameter and morphology of the final product.
Needles:
One of the most common methods of increasing the throughput of the electrospinning process is to add more needles. The increase in the number of needles, from one to many, brings along several other parameters that need to be monitored and controlled. These include the applied voltage and flow rate.
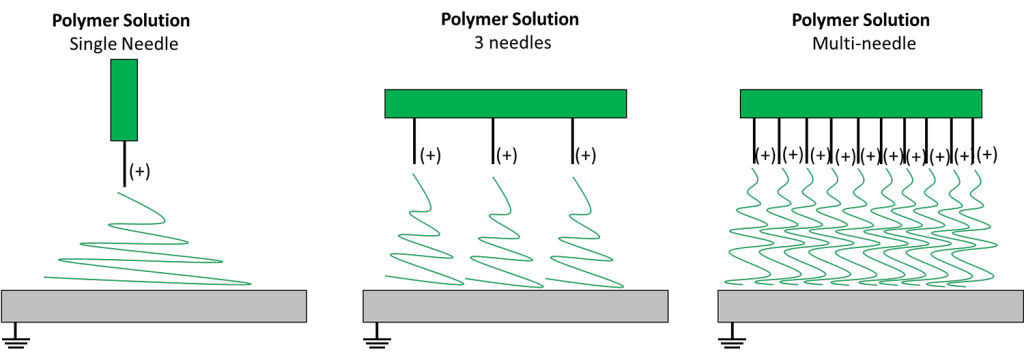
Applied voltages:
The addition of needles causes the electric field from adjacent needles to generate a repulsive force. This force is more pronounced as the number of needles increases and the spacing between the needles decreases. To overcome this repulsive force, the voltage applied to the needles has to be increased. The applied voltage increases non-linearly with the increase in number of needles. The highest increase will be required with the addition of the first few needles to the single-needle setup, with smaller increases required for further increases in needles. Another way to overcome the effects of the repulsive force from adjacent needles is to apply a negative charge to the collector and increase the attractive forces towards the collector.
Flow rate:
Before scaling up the electrospinning process, the flow rate is typically optimized with a single-needle apparatus. Increasing the number of needles will require a proportional increase in the overall flow rate. In general, a 10-fold increase in the number of needles will require a 10-fold increase in the flow rate. This is to keep a constant flow rate per needle. When a low number of needles are used, typical electrospinning systems use a small volume syringe with a syringe pump to control solution flow. As the number of needles increase, the syringe should be replaced with a large volume vessel and the syringe pump replaced by an air pressure line or a peristaltic pump to maintain the required flow rate.
Translating Emitters and Collectors:
Needles:
A key aspect of fabricating large-scale fiber mats is continuous, even deposition. Stationary needles can result in streaky deposition of the fibers perpendicular to the needle axis (Figure 2A). One method to overcome this issue is to translate the needles along the needle axis. This can improve the deposition of the fibers to resulting in a smooth continuous mat (Figure 2B)
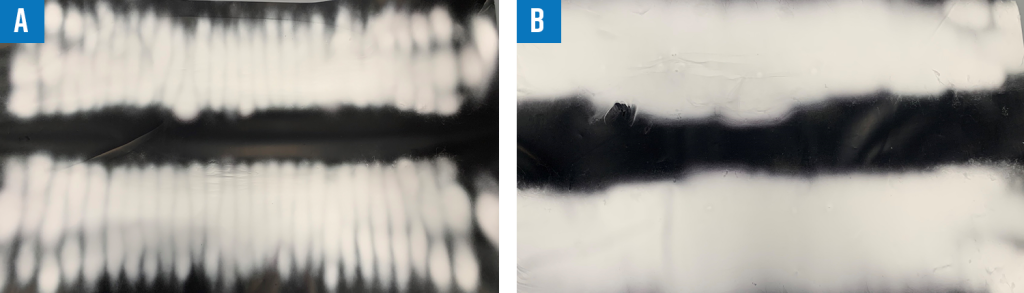
Collector:
The production of electrospun fibers as a continuous batch in a rolled format is key to industrial applications. To achieve large format substrates the deposition of electrospun fibers can be fabricated continuously on a roll-to-roll collector that moves perpendicular to the needles. Figure 3A shows an example setup of a roll-to-roll collector with translating needles. This setup has been used to demonstrate the fabrication of nanofiber mats greater than 1 meter in length and approx. 250 microns thickness in under 2 hours.
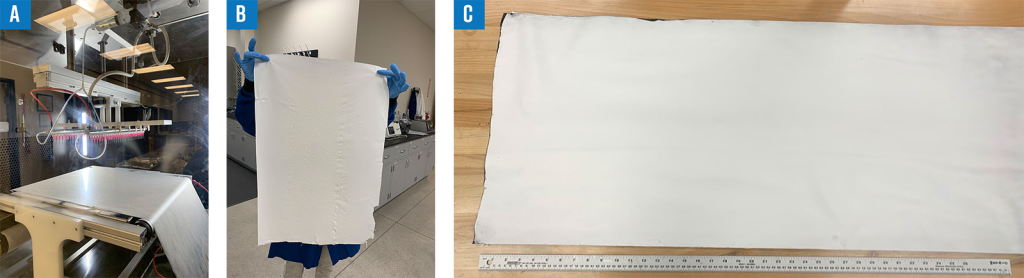
To confirm the uniformity of the fabricated nanofiber mat, the diameter of the fibers and the thickness of the mat were measured at various locations as denoted in Figure 4A. This fiber mat had minimal variation in average fiber diameters, and thickness analysis revealed a uniform mat with an average thickness of 259 µm ± 4.6%. The results are summarized in Figure 4B & C.
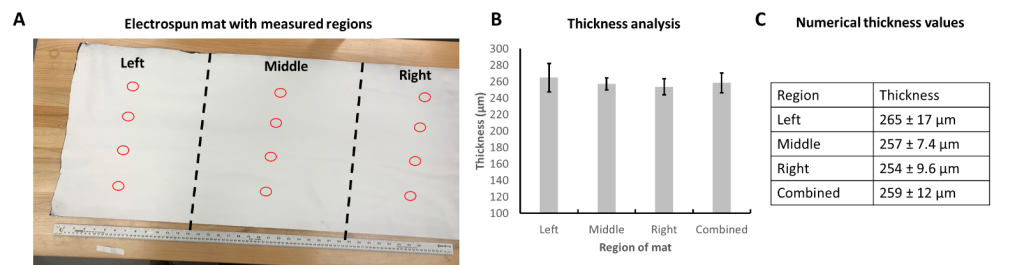
Manufacturing Fiber Sheets:
To increase the throughput, a 180-needle setup on the electrospinning apparatus was used (Figure 5A). The flow rate, applied voltage, and environmental conditions were all optimized for the new setup. Developing a process that improved the rate of deposition allowed for a true continuous process, where the roll-to-roll collector was used to manufacture a 10-meter-long electrospun fiber sheet (Figure 5B). Increasing the needle count from 60 to 180 resulted in a 300% increase in throughput. This displays the versatility and capabilities of electrospinning to scale up nanofiber production for industrial applications.
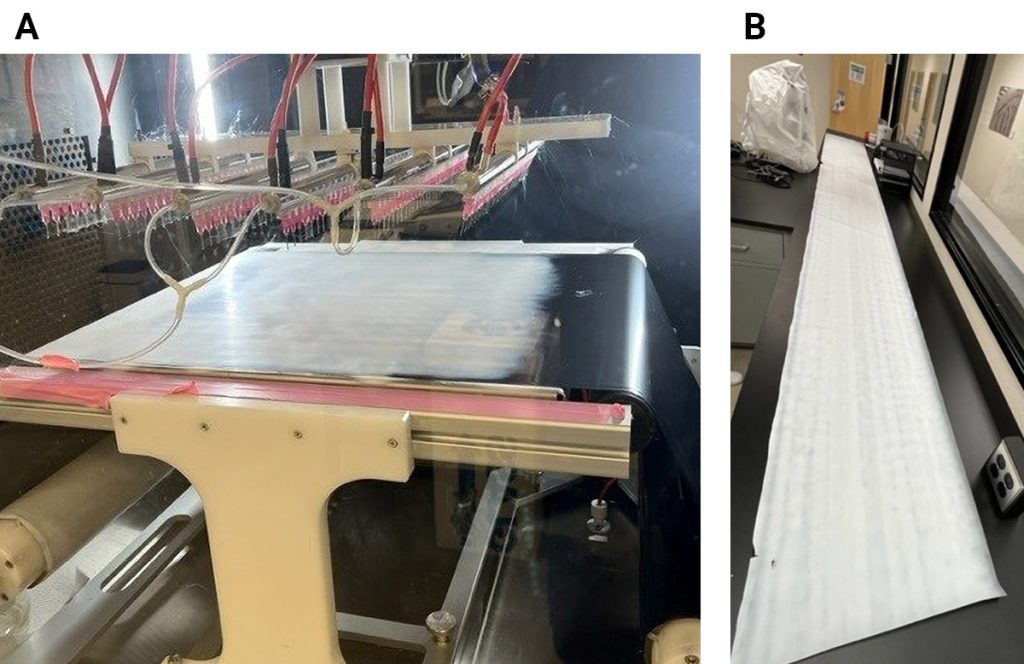
Conclusion:
Electrospinning is a scalable process for producing nano to microscale fiber sheets. By increasing the number of needles and flow rate, fibers are deposited in a high throughput apparatus. This allows for a much faster rate of fiber deposition for commercial applications. Furthermore, translating the needle and using a conveyer roll-to-roll collector significantly expands the area of fiber deposition and allows for the generation of a uniform mat that produces a uniform fiber sheet that exceeds a meter in length. Scaling up the electrospinning process can be optimized for any solution that requires a significant increase in throughput for manufacturing. This is suitable for a variety of industries that range from textile/fabrics, filtration, medical devices, and more.